Deleted
Deleted Member
Posts: 0
|
Post by Deleted on Jan 16, 2020 14:39:14 GMT -6
Thought I would start this off with one of my home made tools. I had built cars for a lot of years and had to make tools for jobs I was doing. One reason was there was no tool and the second reason I could not afford the tool. LOL! So that carried on into guitar building.
I made this simple tool for filing the fret ends at 30 and 45 degrees.
I used some poplar the I had laying around. I cut two grooves in it. 45 and 30 degrees. I found over time these were the two I was using the most.
I used my router table and a round over bit and rounded over the top edges to make it easy on the hand. I have ued this tool for a lot of years now. Still works like it should. It has done a whole lot of frets. I got a fine metal fine from the hardware store.
I cut the grooves on my table saw. The saw blade was the right size (thickness) for the file. The file fits good and snug in the slots. The file does not fall out of the groves. The blade on the table saw was a combination blade. I used that blade to make all my neck blanks. I was using long before I had gotten a plainer joiner.
But anyway... What kind of cool tools have anyone on here made to make the job easier. I would like to see what you made. Not store bought ones.
EB
|
|
Deleted
Deleted Member
Posts: 0
|
Post by Deleted on Jan 16, 2020 18:18:31 GMT -6
here is another tool I made. I came up with this to help me glue an acoustic bridge back on a guitar. I have used this tool a bunch of times and it has worked well every time.
I use more then the 2 screws I am showing in the picture.
Here it is all glued back on.
I like how this simple tool works. Nice thing about it is I can keep working on the guitar and not have big clamps in the way. The tool may be hard for someone with big hands. But I have no problem using it. It does a nice job of keeping the pressure even across the bridge.
I made it from a piece of aluminum strip I had laying around. I measured out where to drill the holes. I didn't really need them all. But they are there now. LOL!
The guitar I worked on in the pictures came to me with the bridge off. I had no way of clamping the bridge. I came up with this idea in bed late at night. I don't sleep all that much at night as it is. I fell asleep and came to like at 2am and this image was in my head. HA! So that morning I went out to the shop and made it. I get most of my ideas late in the night.
EB
|
|
|
Post by antares on Jan 17, 2020 3:49:36 GMT -6
Eddie I need to get back home for this. Next week maybe?
e&oe ...
|
|
|
Post by dnic on Jan 17, 2020 8:32:34 GMT -6
Agreed Eddie, guitar building and repair require a lot of tool making on the fly. I have have built my own versions of those same two tools. I made a bridge clamp for a guitar with no sound hole and only access through the pre-amp hole.
|
|
Deleted
Deleted Member
Posts: 0
|
Post by Deleted on Jan 17, 2020 16:40:21 GMT -6
Agreed Eddie, guitar building and repair require a lot of tool making on the fly. I have have built my own versions of those same two tools. I made a bridge clamp for a guitar with no sound hole and only access through the pre-amp hole. Seems we came from the same era, in that we know at times you just have to make the tool you need. For me it's a lot more fun to make them and have it work out.
I come form the old ways of building cars. Back in my day, I had to make mounts and even made my own frames, there were no go and buy it already done. I see so many people these days that go out and buy want they need.
I know in some ways it may be nice to buy something that "should" work. But There is hardly any craft left in it.
Like building guitars. There are more and more people buying CNC machines. Some of the FB pages I am on a lot of them have CNCs. Again what fun is that? There is one guy who make a bunch of necks. All of them done on a CNC. He sells them on Reverb and eBay and the FB marketplace. Guess he is doing pretty well with it. But to me, even though he makes them out of all kinds of woods, it gets boring to me. Same thing day in and day out.
One of my favorite things in guitar make was hand carving the neck. Yes I know at one time I had tool to help make some things better. Like thickness sanding and a drill press and so on. But with them tools you still need to how to do the craft.
I didn't mean to go on. But I am passionate about the craft of building.
I got into printing back in 1969 while still in high school. Back in them days it was called a craft. But over the years that craft is now gone. Due to computers and 4 color copiers you can now get in a few hours what would take days to craft. Sad in a lot of ways.
As more and more people are able to buy things like CNCs I can't help but wonder how much of real guitars (craft) has been lost. I know there are (I hope) people that will will still make guitars and other wood working that will keep the craft alive for a long time to come. It's just sad to see so many not wanting to make things with their hands, and relying on CNCs and lasers to do the work.
Guess I am just an old diehard...
EB
|
|
|
Post by antares on Jan 17, 2020 17:45:53 GMT -6
Making something out of other things is either in your blood or it's not. About 15 years ago, I left off making things for a living to go into quality assurance. It was a bad choice for one such as myself, but it gave me opportunities that I would otherwise have missed out on, and it also came along at just the right time for weakening joints. I can't get rid of all my tools but I now accept that most of them will never see active service again. It's a funny old world at times.
e&oe ...
|
|
Deleted
Deleted Member
Posts: 0
|
Post by Deleted on Jan 18, 2020 15:07:56 GMT -6
Making something out of other things is either in your blood or it's not. About 15 years ago, I left off making things for a living to go into quality assurance. It was a bad choice for one such as myself, but it gave me opportunities that I would otherwise have missed out on, and it also came along at just the right time for weakening joints. I can't get rid of all my tools but I now accept that most of them will never see active service again. It's a funny old world at times. e&oe ...It is a funny old world.
One of my favorite tools that I still have is the old hand drill. I like using it when ever I can. For me there is something using that old drill and being able to control the speed of the drill.
Just like carving guitar necks. To me there is nothing like using a spoke shave or pull knife and forming wood into a guitar neck. For me there is something that happens to me when I would carve a neck and form it.
It's the best part of building a guitar to me. I would even have my customers come by when it came to shaping the neck. I would shape each neck to what the customer wanted while they were standing there.
You know that my customers got a kick out of seeing how a neck of a guitar came to life. It was fun to see the look on peoples faces as I got the neck to come closer and closer to what they wanted.
I use to tell people try and get that from Fender or Gibson. LOL!
I always worked close with the customer get give them what they wanted. It was not always what I wanted. But hand tools helped in the experience of building/carving a guitar.
But yes, I know that in some ways we pass on the old and embrace the new. But I still can't get over the idea that we are losing out on a great craft. For me there will always be more to making a guitar than just cutting out the wood and having something that looks like a guitar.
Hand built guitars will always have a MOJO that production guitars will never have.
But anyways... Show some of the tools that you all have made. Even if you don't use them anymore. LOL!
EB
|
|
|
Post by antares on Jan 27, 2020 14:24:41 GMT -6
I'm going to take the thread literally. Over the years I've made many small items of tooling and tools in general. This one is not guitar related, I can only think of one specifically guitar related tool and it's "interesting". I shall dig that one out later ... 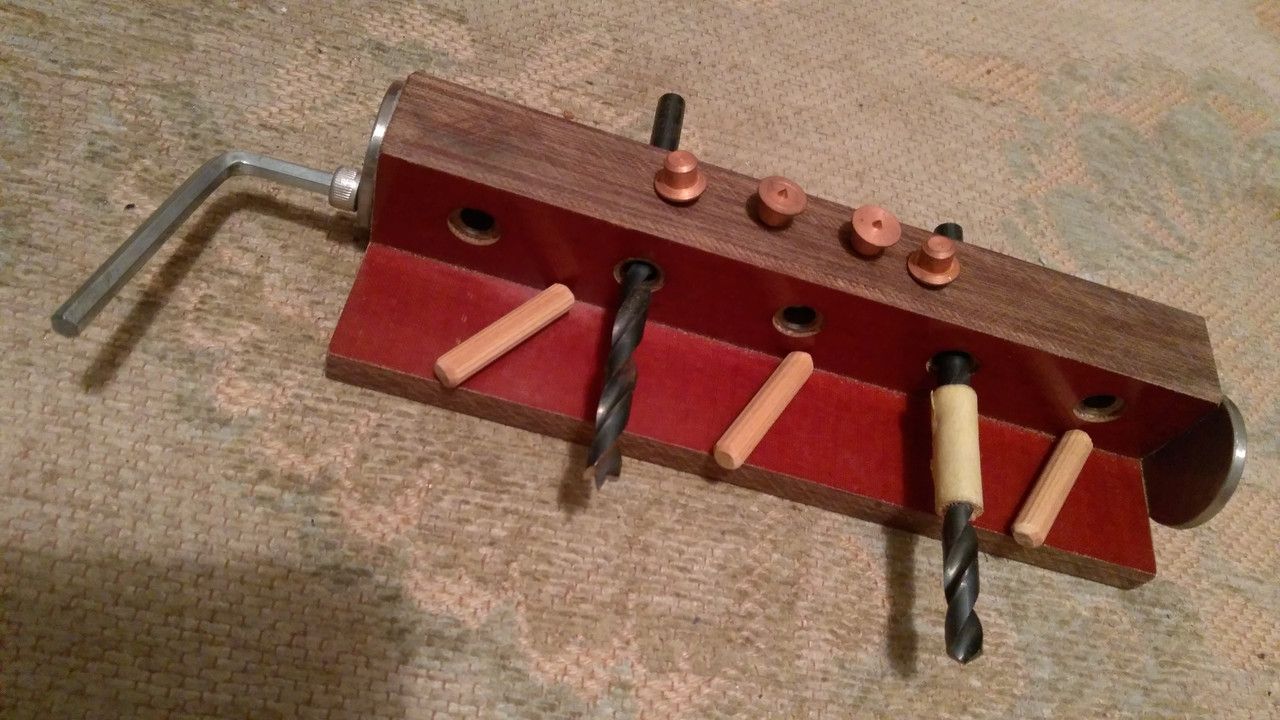 This is one I made for doweling wall shelves onto side supports, but it could be used for a number of different alignment jobs. It is constructed from two pieces of Tufnol joined together with 10-32 UNF MS24693 countersunk machine screws and having heavy gauge swivelling stainless-steel end caps located using MS16998 cap head bolts. One piece of Tufnol has a series of hardened steel bushes pressed in. You can see the 1/4" HSS drill that I ground down to have a centre lead, and a similar plain HSS twist drill. On top are some centre dots that a colleague spun for me on a lathe. In use, you swivel one end cap out of the way and put the tool on the end of a shelf, then you drill through the hardened bushes with the plain drill into the end of the shelf. The masking tape on the the plain drill sets the depth. Then you swivel both end caps and drill the other end of the shelf. Next up you put the centre dots in the end of the shelf and line it up where it needs to go. One whack with a mallet puts centre dots in the side supports. Now you use the centre lead drill to drill the side supports. The dowels go into the holes with some adhesive and you're done. I didn't design it, I saw one for sale at a stupid price and thought "I can do dat!". It's simple and it is foolproof provided you take care. I used PVA and years later after a kitchen refit when I needed to reconfigure the shelf assembly to be a few inches narrower, a swift whack with the mallet separated the assembly at the cost of a handful of dowels. e&oe ...
|
|
|
Post by antares on Jan 27, 2020 14:46:40 GMT -6
Right, I did find it. I said it was "interesting"! Problem: Warmoth wanted a twenty bucks upcharge on a Tele neck for NOT putting the attachment pilot holes in. You know I don't really have words for that. 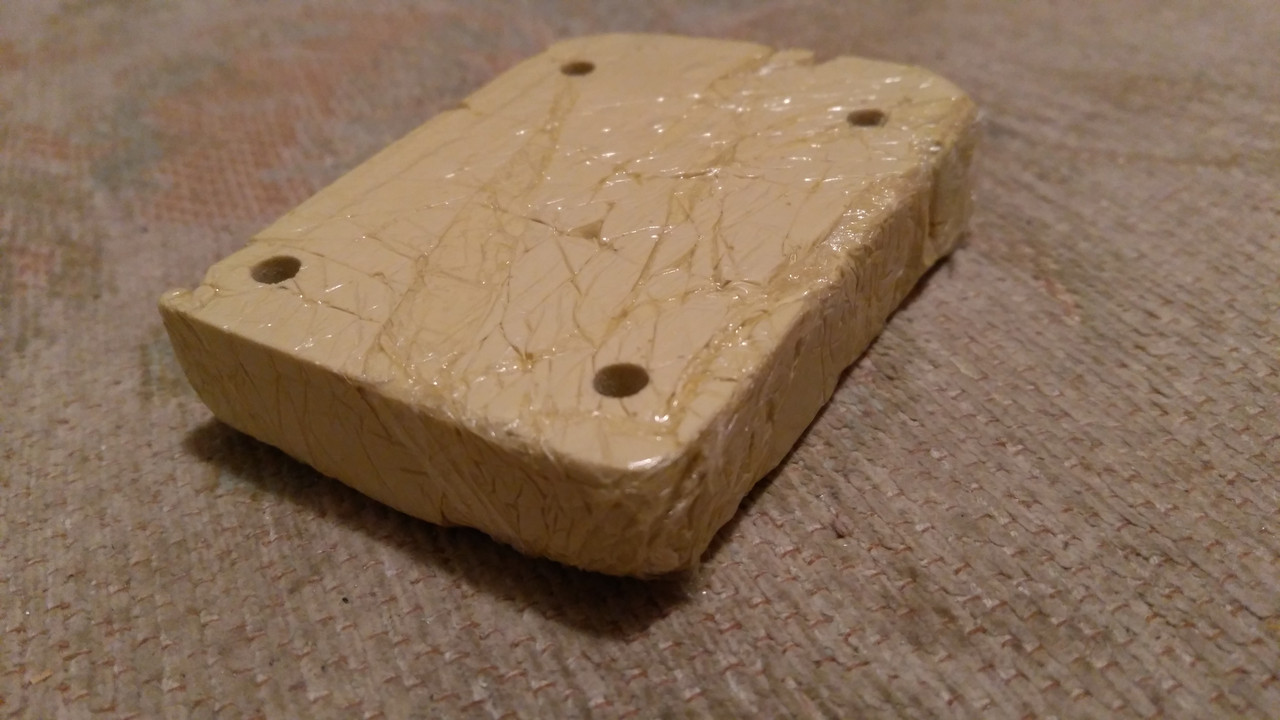 I had a body with no holes drilled anywhere (my Danny Gatton Tele). How to drill holes in the body that will align with the neck? I checked the Warmoth neck in my "Esquire" and the fit was good, so I lined the Esquire neck pocket with chef's Cling Film and packed out the Esquire neck pocket with Aerospace "micro balloon filler". Then I spotted through the body into the now hardened balloon filler and transferred it to the new body. You can still see the cling film on it. I then drilled back through the same holes in the hardened balloon filler into the new body. Job done. It is said that the engineer does with five cents what any fool can do with five bucks? I still haven't forgiven Warmoth, although to be fair, I wanted to buy a celluloid Strat vibrato cover plate in MoTS to match a Warmoth Strat scratch plate I had, but the despatch cost was simply crippling. I telephoned and they fell over backwards to help by sending it off very cost effectively in a Jiffy bag, so they's good guys really ;<D e&oe ...
|
|
|
Post by antares on Jan 27, 2020 14:59:10 GMT -6
Again not strictly a guitar tool, but I've used it loads of times on guitars. It's just a random piece of aluminium 3/4" thick. It has more of those hardened steel drill bushes pressed in. Each hole has two 10mm or 3/8" long (I forget now) bushes in series. They are random sizes in equally random places. They were put in over the years as the need arose. The largest hole is 5/16" and it doesn't "work" because I hammered them in instead of pressing them. In that hole the bushes are not aligned sweet. You can get away with slightly smaller drill but it misses the point. I didn't try to remove them because I figured they would not fit in so tight again. Nothing worse than loose bushes in tooling. Ask me how. (No don't!) I last used this tool to put the wrap around TonePros into my Gordon Smith double cut. That's thd guitar that I reworked from a hummer to a P90. The original bridge was either a Friday afternoon job or it had been intended for a southpaw! It's simple to use, you just hold it down tight and drill with an electric hand drill. Works every time and it's very nearly as good as a pillar drill / drill press. e&oe ...
|
|
Deleted
Deleted Member
Posts: 0
|
Post by Deleted on Jan 27, 2020 18:05:39 GMT -6
Now that is cool! See, that is what I was wanting to see.
I made a jig a long time ago for drilling holes in car frames for my home made engine mounts. LOL!
I use to use my front door as a metal brake. For making fire walls on my hot rods. LOL Thanks for showing your tools! EB
|
|
|
Post by antares on Jan 28, 2020 3:21:49 GMT -6
That reminds me of when I sheared off some sheet metal that was too thin and it just folded over! It was an ancient guillotine with a massive flywheel at one end. I wound it back through it's stroke by using a four foot wrecking bar in the cast iron flywheel. Then I removed the blades and shimmed them up properly. Later I moved to the next (my last) company and we were'n't even allowed to use the guillotine. That always struck me as ridiculous but they said the service engineer told them thd guillotine was the best one he serviced due to the restriction. (ie- no goons shearing off too thin sheet I suppose!)
e&oe ...
|
|
|
Post by dnic on Jan 29, 2020 8:30:47 GMT -6
Those are cool jigs Steve. As you mentioned on the dowel jig you copied it. But the idea doesn't have to be original you just need the wherewith all to replicate it.
So Warmoth needs 20$ to remember to stop the machine before it drills the holes. How special.
|
|
|
Post by GuitarAttack Forum on Feb 2, 2020 13:20:08 GMT -6
Love this thread....great tools and great ideas.
Thanks, Eddie for getting it going and thanks to all for the input.
Looking forward to more posts!
John
|
|
|
Post by dnic on Feb 3, 2020 0:30:13 GMT -6
|
|